Top Packaging Machine Repair Solutions for Enhanced Operational Performance
Top Packaging Machine Repair Solutions for Enhanced Operational Performance
Blog Article
The Ultimate Overview to Product Packaging Device Repair: Keep Your Procedures Running Smoothly
Comprehending the complexities of packaging equipment repair service is critical for maintaining optimum performance and minimizing interruptions. Routine maintenance not just extends the life of these machines yet likewise addresses common problems that can hinder performance.
Relevance of Routine Upkeep
Routine maintenance of product packaging devices is crucial for making sure optimal efficiency and long life. By applying a structured upkeep schedule, drivers can identify possible issues prior to they escalate right into considerable problems. This positive approach not only decreases downtime however additionally extends the life expectancy of the equipment, eventually leading to minimized operational expenses.
Normal inspections enable the analysis of vital parts such as sensors, belts, and seals. Resolving wear and tear immediately protects against unexpected failings that could interfere with production and result in expensive fixings. Additionally, routine maintenance assists make certain compliance with sector standards and policies, promoting a safe workplace.
Moreover, upkeep tasks such as lubrication, cleaning, and calibration substantially enhance equipment effectiveness. Boosted performance equates to constant product top quality, which is vital for preserving client satisfaction and brand track record. A properly maintained packaging equipment runs at ideal speeds and lowers material waste, contributing to overall performance.
Common Packaging Maker Problems
Packaging equipments, like any type of complicated machinery, can experience a range of common problems that may impede their efficiency and efficiency - packaging machine repair. One prevalent trouble is inconsistent sealing, which can bring about item spoilage and wastage if plans are not effectively sealed. This often results from misaligned elements or used securing components
An additional frequent concern is mechanical jams, which can take place as a result of international things, worn parts, or inappropriate alignment. Jams can create hold-ups in manufacturing and boost downtime, inevitably influencing general efficiency. In addition, electronic breakdowns, such as failure in sensors or control systems, can disrupt operations and lead to inaccurate dimensions or unpredictable equipment actions.
In addition, problems with item feed can also occur, where products might not be provided to the product packaging area constantly, creating disturbances. Wear and tear on belts and rollers can lead to suboptimal efficiency, calling for prompt attention to avoid further damage.
Understanding these usual issues is essential for preserving the stability of packaging procedures, guaranteeing that machinery runs efficiently and successfully, which consequently helps in meeting production targets and preserving item high quality.
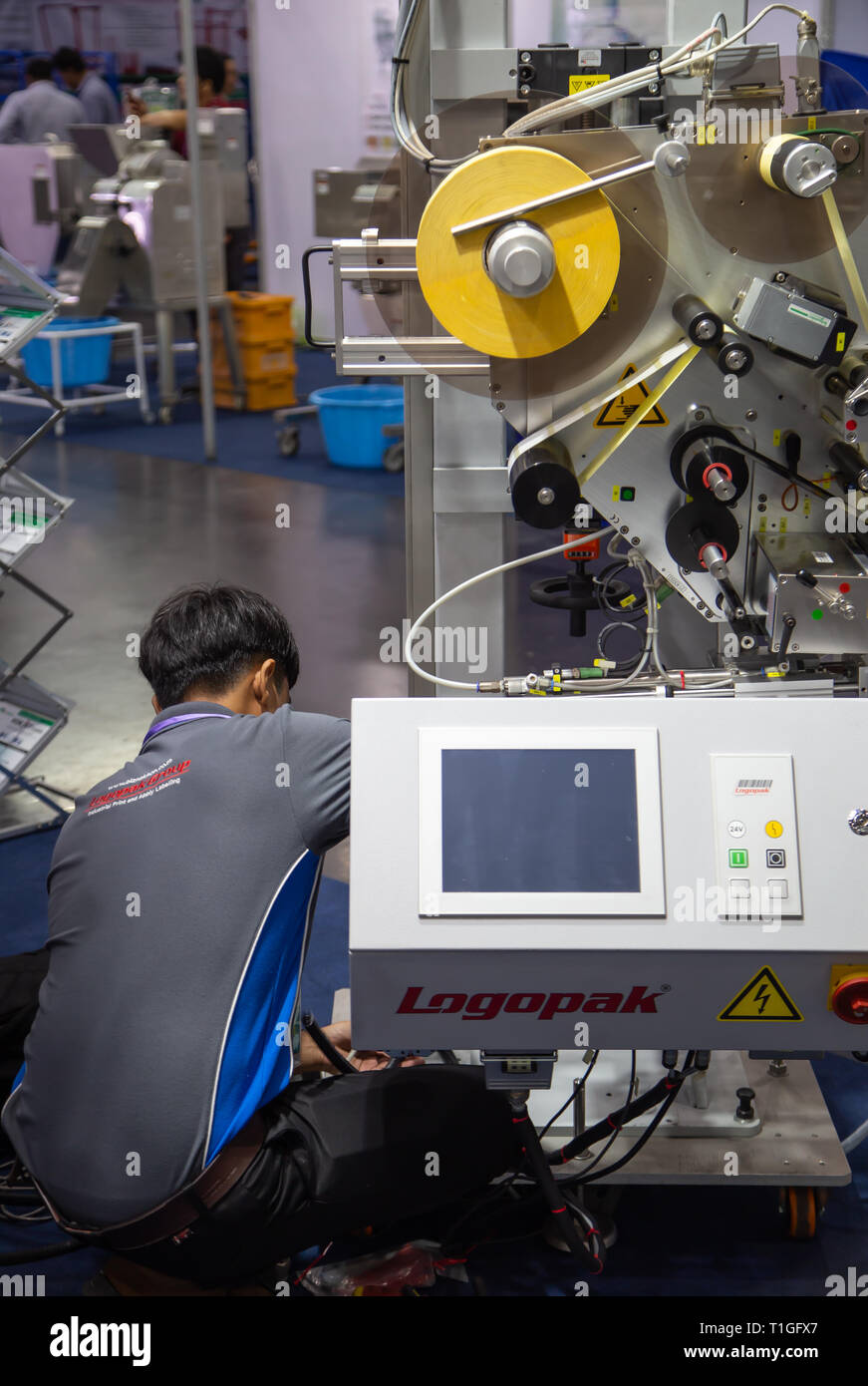
Troubleshooting Methods
Effective repairing techniques are crucial for quickly dealing with problems that develop with packaging machines. A systematic technique is crucial for recognizing the source of breakdowns and minimizing downtime. Begin by gathering info concerning the signs and symptoms observed; this may include unusual sounds, operational hold-ups, or error codes displayed on the machine's user interface.
Following, describe the device's handbook for troubleshooting guidelines specific to the design concerned. This source can offer important insights right into common page issues and suggested diagnostic steps. Utilize aesthetic assessments to examine for loosened connections, worn belts, or misaligned components, as these physical factors commonly add to operational failures.
Carry out a procedure of elimination by screening individual device functions. If a seal is not developing correctly, analyze the sealing system and temperature settings to determine if they satisfy operational specs. Record each step taken and the outcomes observed, as this can aid in future troubleshooting initiatives.
Repair vs. Substitute Decisions
When encountered with tools malfunctions, making a decision whether to repair or replace a packaging equipment can be a complicated and essential option. This decision rests on several vital factors, including the age of the device, the level of the damage, and the projected effect on functional performance.
To start with, consider the device's age. Older makers may need even find out more frequent visit this site fixings, causing greater advancing prices that can exceed the financial investment in a new system. In addition, evaluate the extent of the breakdown. Small problems can frequently be settled swiftly and affordably, whereas comprehensive damage may demand a substantial financial dedication for fixings.
Operational downtime is another important consideration. Spending in a brand-new maker that uses improved effectiveness and integrity might be a lot more sensible if repairing the device will certainly create extended hold-ups. Consider the accessibility of components; if substitute parts are hard to come by, it may be much more calculated to change the equipment totally.
Ultimately, performing a cost-benefit analysis that includes both long-lasting and immediate effects will certainly assist in making an educated decision that aligns with your monetary restraints and operational goals. (packaging machine repair)
Precautionary Procedures for Longevity
Secret safety nets include regular lubrication of relocating components, alignment checks, and calibration of controls and sensing units. Establishing a cleansing routine to eliminate particles and pollutants from equipment can substantially minimize damage (packaging machine repair). In addition, monitoring functional criteria such as temperature and resonance can assist find irregularities beforehand
Training staff to identify signs of wear or breakdown is an additional crucial component of preventative maintenance. Encouraging drivers with the understanding to execute standard troubleshooting can cause quicker resolutions and minimize functional disturbances.
Paperwork of maintenance tasks, including solution documents and assessment findings, cultivates liability and helps with educated decision-making pertaining to replacements and repairs. By prioritizing preventative actions, companies can ensure their packaging equipments run at peak efficiency, inevitably leading to boosted performance and minimized functional costs.
Verdict
In final thought, the reliable maintenance and fixing of packaging equipments are critical for sustaining functional efficiency. By executing preventative actions, businesses can enhance equipment longevity and ensure nonstop productivity in packaging procedures.
Recognizing the ins and outs of packaging device fixing is crucial for preserving optimal efficiency and decreasing disruptions.Regular upkeep of product packaging devices is crucial for making sure ideal efficiency and long life.Product packaging machines, like any type of intricate equipment, can run into a variety of typical problems that might hinder their performance and efficiency. If repairing the machine will certainly cause long term hold-ups, investing in a new maker that supplies enhanced effectiveness and integrity may be more prudent.In final thought, the effective upkeep and repair of packaging makers are paramount for maintaining functional effectiveness.
Report this page